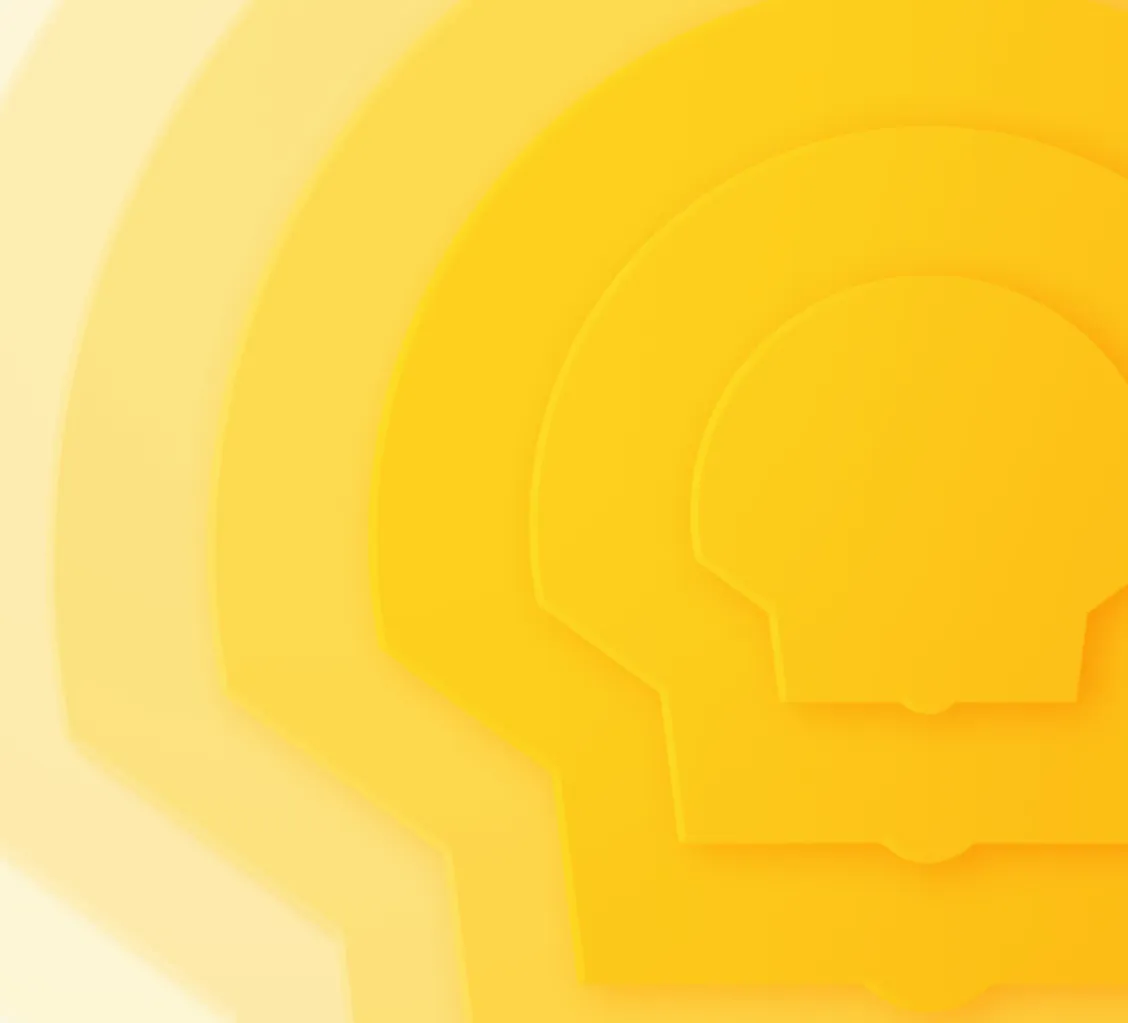
Master Data Analyst
Where you fit in?
The Lubricants Americas Business is on a transformational journey to grow our business by 20% in the next 3 years - enabled by a broader digital transformation, a S&OP refresh, and brilliant basics amongst many other tactics – all of which are underpinned by accurate, dynamic, master data. The business has over 10k ship-to locations, 20+ manufacturing locations, 10+ storage locations, 4k+ finished goods, 1k+ raw materials with thousands of different shipping lanes, vendors, etc. – all this to say there is a significant amount of master data to be maintained in constantly evolving external market conditions.
For us to not only be cost competitive, but also to deliver against our customer promise, and leverage the various digital tools being implemented – our master data accuracy must grow significantly and fast.
Vision: To take our E2E Master Data Mgmt from Emerging to Differentiated on the Accenture Maturity scale – distinguished by leveraging proactive alerts to address master data anomalies, incorporating financial inputs into master data management, and development and use of in depth business rule sets to audit and update rule sets.
This position is for 1 of 4 Master Data Analysts – each of which will have a primary focus:
- Planning: FG Production and Sourcing
- Planning: Raw Materials & Vendors
- Logistics: Customer Sourcing
- Documentation of Processes
What’s the role?
- Establish and maintain a continuous process for tracking master data activities, including request volumes and cycle times, as well as monitoring data quality metrics.
- Collaborate with stakeholders to prepare and distribute monthly data quality reports, identifying root causes of inconsistencies and implementing corrective actions.
- Partner closely with stakeholders to ensure master data accurately reflects end-to-end business operations.
- Assess the business impact and opportunity costs associated with poor data quality.
- Support the deployment of new modules, system releases, and projects by ensuring timely and accurate data creation or updates.
- Conduct data quality reviews to ensure material master data aligns with internal policies, procedures, SAP requirements, and downstream system needs.
- Ensure consistent and accurate maintenance of master data across all platforms, including SAP, GPC, O8, and TMS.
- Develop and implement methodologies to dynamically update master data based on rule sets and performance comparisons, ensuring systems reflect actual business performance.
- Utilize analytics tools such as Power BI and Spotfire to detect data anomalies and drive corrective actions, using automation tools like Alteryx for mass updates across systems.
- Analyze and resolve business issues within defined service level agreements (SLAs), ensuring alignment with internal and external customer expectations.
- Maintain and update documentation of approved best practices and provide support and coverage for team members as needed.
FG Production & Sourcing
- MDM Master Data Fields (support both introductions and withdrawals)
- MRP 1, 2, 3 Master Data Fields
- Production BOM Consistency Checks (Production, Sales BOM, Routings, etc.)
- Accurate Plant & Sales Org setup
- Production Capacity Run Rates (Gallons/Minute, Bottles/Minute, etc.)
- Asset Capacities (Tank, Loading Rack, Blending/Packaging, WH)
- Sourcing – Inter/Intra company and External/Contract (including PIR, OA, etc.)
- Costing & Production Lot Sizes
Raw Materials & Vendors
- MDM Master Data Fields (support both introductions and withdrawals)
- MRP 1, 2, 3 Master Data Fields
- Vendor Lead Time Tables and Transits
- Sourcing – Inter/Intra company and External/Contract (including PIR, OA, etc.)
- Cost information maintained accurately
Customer Sourcing
- ISOIL Table Mgmt
- DLT4X: Leadtime Table Mgmt
- Route Monitoring/Management across FTL, LTL, Bulk, Pack
Setup of T-Zones to minimize split sourcing, complex T-Zones, etc in an effort to minimize cost and manual source changes
What we need from you
- Any Bachelor’s Degree in Engineering, Supply Chain Management, Logistics, or Business.
- 3-5 years’ experience in a supply chain environment
- 1-3 years SAP experience / ERP experience required with strong exposure to at least one of the functional areas described above
- Self-starter with the ability to work independently with little supervision.
- Open-minded and open to change
- Excellent problem-solving abilities.
- Strong attention to detail, accuracy, and follow-through.
- Strong analytical, numerical, math, statistics skills.
- Ability to cooperate and work in multicultural environment.
- A high level of organizational and communication skills is required