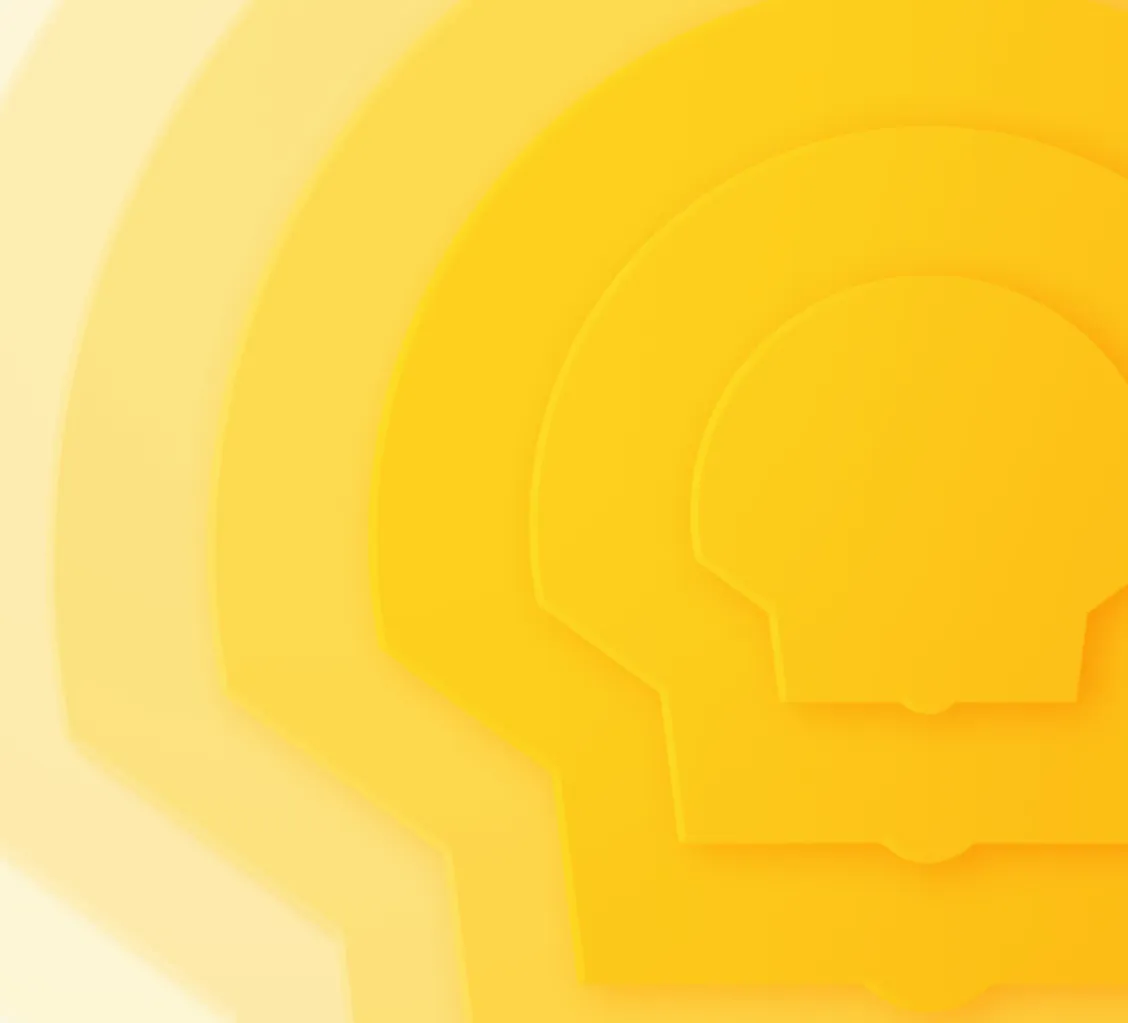
Senior Process Control Engineer APC
Where you fit
1. Responsible for SMDS Process Control & Automation mainly for the site. This includes the development, support and maintenance of the base layer controls, the advanced process controls and the instrumented protection functions, with the objective of ensuring a safe, reliable, environmentally sound, optimized and energy efficient day to day operation of SMDS complex.
2. Lead for Advanced Process Control – responsible for the setting up, design and implementation.
3. Responsible for keeping up to date the related controlled documents: Process Control Narratives, Safeguarding (IPF) Narratives and Cause and Effect matrices.
4. Support ESP (Ensure Safe Production) operation team to achieve the target KPIs for alarms and operator interventions
5. Support operation training by designing and maintaining the Operator Training Systems (OTS)
6. Maintain the various L2/L3 Process Control Domain (PCD) components and applications including OPC, Plant Information, Alarm Management and APC.
What's the role?
1. Provide support for all process control related matters, including base layer, PI plant information, process safeguarding and alarm management for SMDS.
2. Setting up and implement APC for SMDS.
3. Responsible for all Advanced Process Control (PACE, SMOC and RQE) applications by monitoring performance based on uptime and compliance of the controllers on daily basis.
4. Maintain Process Control Narratives and responsible for the upkeep of the process control narratives up-to-date.
5. Maintain Safeguarding (IPF) Narratives for SMDS complex and responsible for the upkeep of Safeguarding (IPF) Narratives up-to-date.
6. Maintain the Cause and Effect (C&E) matrices and responsible for the upkeep of the C&E up-to-date.
7. Site focal point of MDPro system application. Monitor process control performance and key performance indicators and implement corrective measures to improve performance in process units and complex level to Shell group standard.
8. Advise operations on process control tuning and configuration in order to maintain stable, efficient and reliable process unit operations. Provide process control trouble shooting and solutions on investigation to process upsets and defects.
9. As Technical Authority (TA3) for Process Control & Automation Systems and Alarm Management Design under SMDS Technical Authority Framework, provide process control and safeguarding inputs/review to plant changes as required per SMDS MOC plant change procedure and be responsible for the process control design of plant changes in the SMDS complex.
10. Identify and resolve control performance problems by coordinating with others in areas of specialization (instrumentation & control system, analyzers, process, mechanical equipment, laboratory, IT, etc). Participate in unit reviews, management of change, HAZOP and root cause failure analysis as needed.
11. Provide knowledge sharing for operators training on Process Control.
12. Perform functional testing on control and safeguarding loops during commissioning and start up (IPS/DCS).
Role requirement
- Bachelor/Master or higher degree in Chemical Engineering or relevant disciplines with process control specialization is highly desirable.
- Relevant working experiences in process control and automation disciplines.
- A minimum of 5 years of relevant experience in a refinery, gas plant or chemicals site is required, preferably with a well-established track records in advanced process control and PACO TA3 appointment.
- Good track record of consistent top quartile delivery in Process Safety, HSSEQ, production.
- Relevant experience with Yokogawa CS3000 or Centum VP DCS, Honeywell FSC PLC, OSISoft PI, Honeywell DynAMo suite and Honeywell UniSIM Design suite.
- Relevant experience with Advance Process Control (APC) and Real Time Optimisation (RTO) applications and implementation , compressor anti-surge control applications and MDPro
Company Description
Shell has been a partner in powering Malaysia’s progress since 1891 when we established our first depot in the Straits Settlements. Today, we are an integrated energy company comprising Upstream, Downstream, Integrated Gas and New Energies, Projects & Technology, and Shell Business Operations. Shell Malaysia aims to be the leading energy player in the country, powering Malaysia’s future with cleaner, innovative, and competitive energy solutions.
- Upstream
More than a century, Shell has been operating and we continue to extract and deliver oil and gas efficiently, profitably, and in environmentally friendly and socially responsible ways to meet evolving customer needs and the growing demand for energy.
- Downstream
With over 950 service stations, Shell has the leading market share in the fuels retailing business in Malaysia. In Malaysia, we make and sell more than 600 different lubricants for the automotive sector, heavy-duty transport, food processing and power generation. We are the lubricants market leader in Sabah and Sarawak.
- Integrated Gas, Renewables and Energy Solutions
Shell set out its Powering Progress strategy, which we aim to deliver through our three business pillars of Growth, Transition and Upstream. The Growth Pillar includes our Marketing and Renewables & Energy Solutions businesses and focuses on working with our customers to accelerate the transition to net-zero emissions. One of our achievement, Sarawak onshore: World’s first commercial GTL plant (SMDS)
- Project & Technology
As P&T, we exist to make the delivery of Shell’s strategy and the growth of our company possible. P&T works collaboratively and in an integrated way with its business partners, to deliver value for our customers, and for Shell.
An Innovative Place to Work
There’s never been a more exciting time to work at Shell. Everyone here is helping solve one of the biggest challenges facing the world today: bringing the benefits of energy to everyone on the planet, whilst managing the risks of climate change.
Join us and you’ll add your talent and imagination to a business with the power to shape the future – whether by investing in renewables, exploring new ways to store energy or developing technology that helps the world to use energy more efficiently.
An Inclusive & Progressive Place to Work
To power progress together, we need to attract and develop the brightest minds and make sure every voice is heard. Here are just some of the ways we’re nurturing an inclusive environment – one where you can express your ideas, extend your skills and reach your potential.
- We’re creating a space where people with disabilities can excel through transparent recruitment process, workplace adjustments and ongoing support in their roles. Feel free to let us know about your circumstances when you apply, and we’ll take it from there.
- We’re closing the gender gap – whether that’s through action on equal pay or by enabling more women to reach senior roles in engineering and technology.
- We’re striving to be a pioneer of an inclusive and diverse workplace, promoting equality for employees regardless of sexual orientation or gender identity.
A Rewarding Place to Work
Combine our creative, collaborative environment and global operations with an impressive range of benefits and joining Shell becomes an inspired career choice.
We’re huge advocates for career development. We’ll encourage you to try new roles and experience new settings. By pushing people to reach their potential, we frequently help them find skills they never knew they had, or make career moves they never thought possible.